Earlier this year, the Health & Safety Executive (HSE) issued its long-awaited update to fork lift truck safety guidelines entitled: Rider-operated lift trucks. Operator training and safe use. Approved Code of Practice and Guidance (L117).
By Owen Delaney, Technical Manager, Fork Lift Truck Association
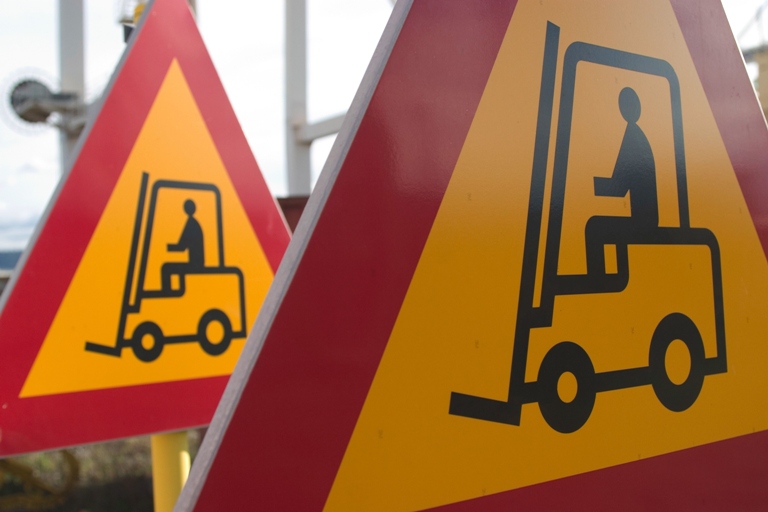
The revised documentation is aimed at employers and those responsible for ensuring safe operations, including those who are in control of worksites. The aim is that employers must meet their legal obligation to ensure that all operators receive adequate training.
L117 outlines the main legal requirements relating to the operation of lift trucks, and contains the Approved Code of Practice (ACOP) and guidance on operator training for stacking rider-operated lift trucks. Importantly, the revised version of L117 clarifies the law for employers and gives the HSE greater powers. While their ability to intervene, and bring a company’s safety up to scratch, is nothing new, they can now charge for the privilege. The new standard fee is £124 per hour to resolve material breaches of the law.
The new documentation incorporates some of the information contained in Safety in working with fork lift trucks (HSG6).
With the updated L117 come four key considerations for those responsible in ensuring safe operations:
- Refresher training
Reassessment allows employers the opportunity to identify and address such lapses before they lead to potentially serious accidents. The new guidelines recommend automatic refresher training or a retest after a set period of three to five years to ensure employees remain competent. There is no legal requirement for fork lift truck operators to receive refresher training at specific intervals. When set refresher training is adopted, managers and supervisors must still monitor performance
Online re-assessment tools, such as Virtual Risk Manager – FLT, enable users to quickly and objectively identify the most at-risk operators, and issue refresher training accordingly. For more information on the benefits of this tool, visit the FLTA website –
www.fork-truck.org.uk
- Supervisor training
The importance of supervisor training is covered by the Health & Safety at Work Act (HSW). However, it is now considered so important, that the L117 now mentions it too. It’s important to note that, unlike some other guidelines, this is a solid requirement:
The HSW Act requires you to provide adequate supervision. It is essential that supervisors have enough training and knowledge to recognise safe and unsafe practices.
- Daily or Pre-shift checks
The revised guidelines state that, at the beginning of each shift, operators should check their lift truck in accordance with the vehicle handbook, and document the findings. Any defects identified which could affect the safe operation of the vehicle must be reported to a supervisor to ensure they are fixed.
Resources to assist in vehicle checks are available through the FLTA online shop.
- Medical considerations
Disabilities (mental or physical) do not automatically disqualify an individual from being a fork truck operator. Fitness for such work should be evaluated on a case-by-case basis, through risk assessment and medical advice.
Guidelines recommend that operators possess a standard of fitness equivalent to that required of an ordinary driving licence. However for more technical work, it is suggested that lift truck drivers possess a level of fitness equivalent to that of a Heavy Goods Vehicle (HGV) licence holder.
The Fork Lift Truck Association is the UK’s independent authority on fork lift trucks. For more information on joining the Safe User Group call 01635 277579 or visit -
www.fork-truck.org.uk
Click here to read the next Editor's pick